Long John anyone?
- attilio24
- Apr 3, 2021
- 4 min read
Updated: Feb 23, 2023
An article of the Scientific American, issue March 1973, revealed that in the animal kingdom, energy efficiency for locomotion varies widely. Birds are in general great at this. Humans suck. Except when they bike. When we bike, we are the most efficient creature for motion. Bikes are soaked with poetry. They were energy efficient tools 100 years ago, before technology disrupted everything and I see some magic in this fact.
Now that we know I like bikes, let me share an early design for this e-Long John. It is designed to be electrically assisted, maintenance free and practical. It is designed for circularity. To live long, to be repaired and reused.
The general layout, in particular the 20" wheels, address practicality. I am the owner a folding bike since 2014, and this wheel size is absolutely adequate in my experience. especially with increased tire shoulders (1.75"). On top of the natural comfort of the 20" wheel, I expect some dampening form the frame and in conclusion, a comfortable ride. In return, we save on overall length (-30cm). I used to carry the bike in tight spaces (garages, backyards etc) and makes it easier to store a dismantled bike.
The solution of the single mainframe tube is to address battery housing. I find the current conversion kits the market offers, even in newly developed frames, to be aesthetically disturbing. This design allows us to keep the battery pack (up to 3KW/h and 18kg) low to the ground and easy to handle. The considerable size of the battery pack is not intended to provide only more energy. It is intended to provide a long-lasting battery and in order to do so, it has to operate and a charge and discharge capacity between 20% and 80%. This is true for battery cell chemistry in the family of Lithium-Ion. This is how Tesla battery packs are designed to be able to lose only 10% capacity over 10 years, while other applications, such as cell phones, struggle to reach 3 years. As I said the bike must have a long life cycle.
To access the battery pack, you need to open the hinged frame. It is a sealed hinge, that allows to fold the frame and reduce the size of the bike when not used or to make it possible to load it on a regular car.

To accommodate such massive battery pack, the classic steering by levers had to go. That steering system is great, however requires the steering tube to go all the way down through the main frame cutting the available volume for the battery. By using a "steer by cable" system we avoid compromises.
Ongoing project...
Updates August 2021
I hired a ream of 4 to build the bike. Nicholas, Sam and Philip, (and me) contributed in different ways to the design of the bike. Some helps with geometries, some helped with suppling components under COVID constraints, some helped with novel and useful solutions to old problems.
You might notice how some details changed as a result of this enormous equation. The front tube hinge disappeared, in favour of a bolted solution. The rear triangle does not have a "split" but a new geometry to let the belt trough. Last but not least the cargo bay is taking shape as a foldable unit.
Materials have been selected as aluminium 6005 for the battery tube and the cargo bay area. This choice will keep weight down to help less powerful individuals (my tiny wife) to handle the bike with ease. The back frame and front frame will be made of steel (unsure what alloy to select for this).
Battery cells were bought 63 days ago form China. The 150 li-ion cells are still somewhere in Kazakhstan. I am not sure they will ever arrive. Time will tell. Battery management system, O-rings, insulation, shrink wrap, special tape etc. are all with me ready to go!

Fabrication of the frame should start in September and assembly should follow after that. Cross your fingers!
October 2021 update
Batteries are here! Voltages are consistent across the lot, and I am confident they will serve us well. The discharge/charge ratings are in line with the expected use of the battery and beyond. The battery is designed to withstand a 2000w continuous discharge. It will not be needed for the motor assist (250W continuous and 800w peak) but will be in the future for accessories applications, like a big ghetto-blaster.
Other components arrived, such as the waterjet cut cargo bay support and hinges. The waterjet keeps the component cold minimising distortions during cut (compared to plasma) and leave a fine surface finish, making is ready to weld in place without further operations and leaving the components with a very accurate geometry.
December 2021 Update
The design was finalized, and the fabrication has begun. Smaller details will be decided on the go as the bike is made. As an example, the location of the cables support.
Now my attention is on the assembly of the battery and the supply of the remaining bike components. From now on the process should accelerate and I would love to see the bike finished in a month from now.
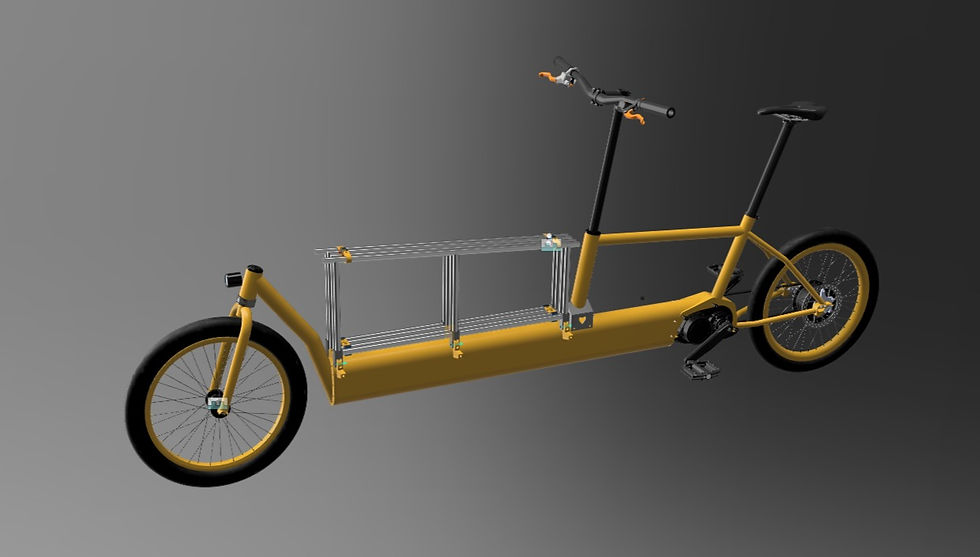
September 2022
GOD progress is so slow! Not my fault! The frame construction has been repeatedly delayed. On my side I can't do much except focusing on what has to come next. The cargo box. The original idea was to have a foldable unit installed on the bike. A frame made of aluminium tubing and walls made of synthetic fabric 300+D. That seemed to take too long to make, and I picked a more classic design (plywood box) as temporary solution.
November 2022
The work on the frame started after a long pause. We tested the battery and wired the harness for lights, motor and screen. We also started welding the battery case which will provide the base to assemble everything else.
February 2023
Done.
Where to go next? How about this
Comments